The Transformative Role of Pressure Die Casting Components in Today's Industry
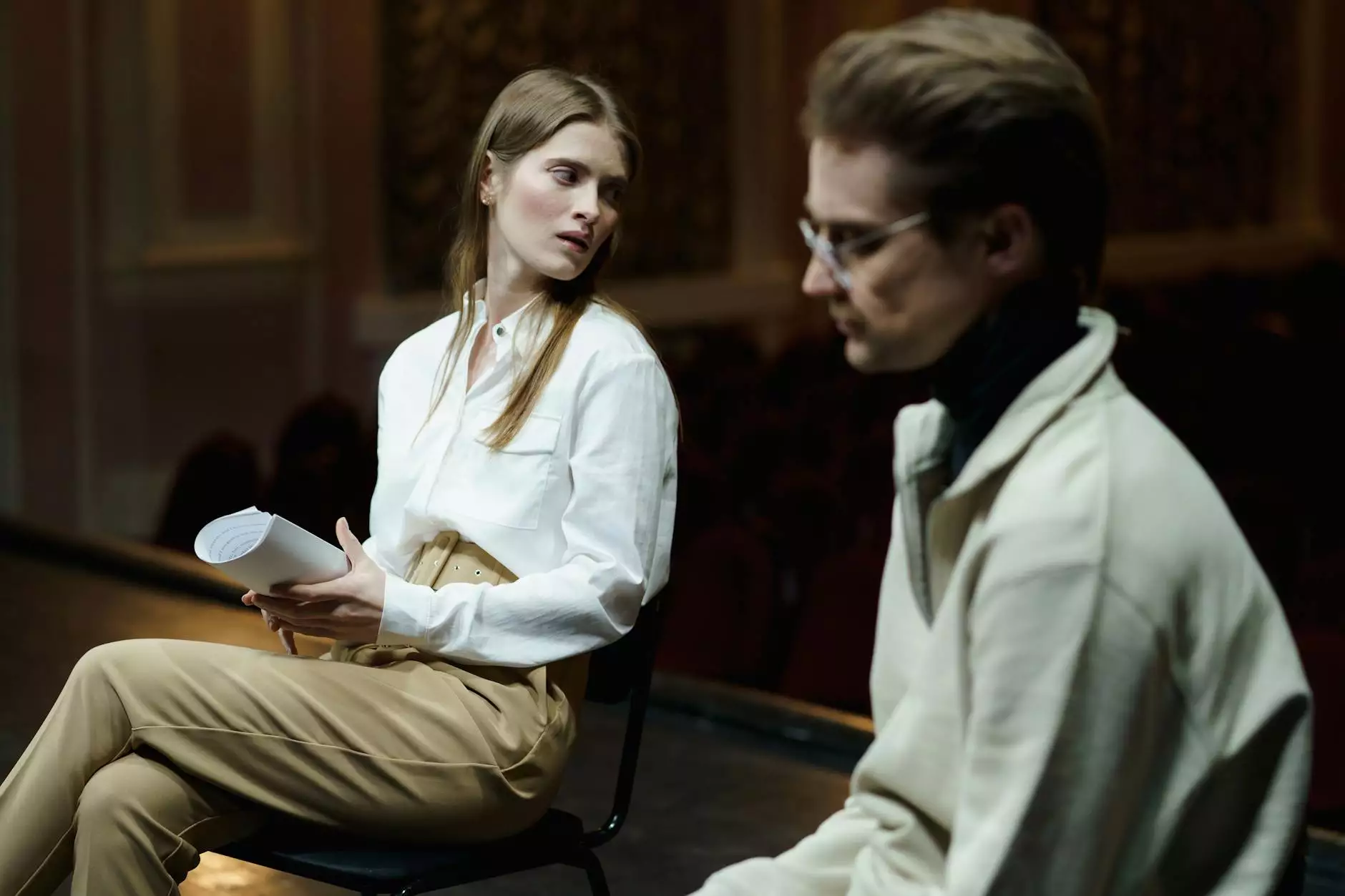
Pressure die casting components are an integral part of various manufacturing processes, contributing significantly to the production of high-quality metal parts. As industries evolve, understanding the advantages and applications of pressure die casting becomes critical for businesses seeking efficiency and innovation. This article delves into the world of pressure die casting, exploring its benefits, applications, and future trends within the metal fabricators category.
What is Pressure Die Casting?
Pressure die casting is a manufacturing process that involves forcing molten metal into a mold under high pressure. This method is particularly advantageous for producing complex shapes with high precision. The process is typically used for metals like aluminum, zinc, and magnesium.
The Process of Pressure Die Casting
The die casting process can be broken down into several key steps:
- Preparation: The mold is prepped for casting, including temperature control to ensure optimal conditions.
- Melting: Metal is heated to its melting point, transforming it into a liquid state.
- Injection: The molten metal is injected into the mold under high pressure, filling all cavities and ensuring a tight fit.
- Cooling: The metal cools and solidifies within the mold.
- Extraction: Once cooled, the mold is opened, and the final component is ejected.
Benefits of Using Pressure Die Casting Components
Utilizing pressure die casting components offers numerous advantages that enhance manufacturing efficiency and product quality.
1. Precision and Accuracy
One of the standout features of pressure die casting is its ability to produce parts with high precision and tight tolerances. This precision is vital in industries such as aerospace and automotive, where every component must meet strict specifications.
2. Enhanced Surface Finish
Parts produced through the pressure die casting process often exhibit a superior surface finish, minimizing the need for further machining and reducing production time and costs.
3. Strength and Durability
Components made with pressure die casting techniques are known for their high strength-to-weight ratio. The rapid cooling of the metal in the dies enhances the mechanical properties, making the components durable and reliable in critical applications.
4. Cost-Effectiveness
Despite the initial investment in die creation, pressure die casting can be cost-effective in high-volume production due to reduced cycle times and minimal waste.
5. Design Flexibility
The process allows for an array of design options, accommodating complex geometries that might be unattainable via other manufacturing methods.
Applications of Pressure Die Casting Components
Pressure die casting components have found their way into various industries, proving their versatility and reliability.
Aerospace Industry
In the aerospace sector, where safety and performance are paramount, pressure die casting components are used for lightweight but robust parts, ensuring structural integrity while minimizing weight.
Automotive Industry
Automotive manufacturers utilize pressure die casting for components like engine blocks, transmission housings, and intricate detailing, where precision is critical to vehicle performance.
Electronics
The demand for lighter and more efficient electronics has led to the incorporation of die-cast components in various devices, emphasizing their adaptability and efficiency.
Industrial Equipment
Many industrial machines benefit from the reliability of pressure die casting components, which can withstand rigorous application demands.
The Future of Pressure Die Casting Components
As technology advances, the future of pressure die casting components looks promising. Several trends and advancements are shaping the industry:
Technological Innovations
With the rise of Industry 4.0, automated systems and IoT integration in die casting machinery is enhancing precision and efficiency. Smart factories are adopting real-time data analytics to optimize production processes.
Environmental Sustainability
Pressure die casting is becoming increasingly eco-friendly. Manufacturers are exploring ways to reduce energy consumption and minimize waste during production, aligning with the global push towards sustainability.
Material Advancements
Research into new alloys and composite materials will likely lead to even stronger and lighter components, broadening the scope of applications for pressure die casting components.
Choosing the Right Partner for Pressure Die Casting
Selecting a reputable partner for your pressure die casting needs is crucial to ensure quality and reliability. Factors to consider include:
- Experience: Look for a provider with a proven track record in pressure die casting.
- Quality Control: Ensure they have stringent control processes in place to maintain standards.
- Technological Capability: Assess their machinery and technology to guarantee modern practices.
- Customer Support: A good partner should offer excellent customer service and support throughout the project.
Conclusion
Pressure die casting components play a vital role in modern manufacturing, providing unparalleled precision, strength, and efficiency. As industries continue to evolve and demand higher performance from their components, understanding the significance of pressure die casting will be essential for businesses in the metal fabricators category. By embracing this innovative manufacturing process, companies can enhance their production capabilities and remain competitive in a dynamic market.